- The Role of BI in the Manufacturing Industry
- Key Integrations of Business Intelligence in Manufacturing
- ERP Systems
- Supply Chain Management
- IoT Devices
- Quality Management Systems
- Customer Relationship Management (CRM)
- Human Resource Management Systems (HRMS)
- SCADA Systems
- MES (Manufacturing Execution Systems)
- EAM (Enterprise Asset Management)
- Benefits of Business Intelligence for Manufacturing: Unlocking Enhanced Efficiency and Collaboration
- Enhanced Quality Control
- Supply Chain Optimization
- Data-Driven Decision Making
- Enhanced Collaboration
- Cost Reduction
- Improved Operational Efficiency
- Use Cases of Business Intelligence for Manufacturing
- General Electric (GE) Employment of Predictive Maintenance
- Siemens’ Global Business Services
- Boeing’s Implementation of BI for Quality Control
- Toyota’s Production Efficiency with BI
- Intel’s Utilization of BI for Analyzing Supply Chain Data
- Best Practices of Adopting BI For Manufacturing
- Set the Stage and Craft Clear BI Objectives
- Engage Key Players or Stakeholders
- Invest in Data Quality
- Choose the Right BI Tools
- Start with a Phased Approach
- Monitor and Iterate
- Integrate with Existing Systems
- Train Your Team
- Monitor and Measure Progress
- Implementing BI in Manufacturing: Key Challenges and Practical Solutions
- Change Management
- Data Integration
- User Adoption
- Data Quality
- How Can Appinventiv Help You in Leveraging Business Intelligence to Make Data-Driven Decisions for Your Manufacturing Business?
- FAQs
As the manufacturing sector becomes increasingly intricate, leveraging data effectively has never been more critical. Manufacturers today navigate a labyrinth of processes, technologies, and human capital, all while striving for greater efficiency and innovation. This is where business intelligence for manufacturing emerges as a game-changer. By transforming complex datasets into actionable insights, BI enables organizations to make informed decisions that drive performance and productivity.
It empowers manufacturers to streamline operations, anticipate market trends, and enhance customer satisfaction. As the industry embraces BI tools, the focus shifts from reactive measures to proactive strategies, allowing businesses to stay ahead of the competition. In a world where data reigns supreme, integrating business intelligence in the manufacturing process is not just an option; it’s a vital step toward sustainable success and growth.
In this blog, we will delve into the pivotal role of BI for manufacturing. We’ll cover essential integrations, explore the numerous benefits, and present real-life use cases that illustrate its impact. Additionally, we’ll outline best practices for successful BI implementation in manufacturing and address the challenges that may arise. Let’s get started!
The Role of BI in the Manufacturing Industry
Business Intelligence (BI) is essential in the manufacturing industry, transforming raw data into meaningful insights. It enables manufacturers to analyze large datasets from production lines, supply chains, and customer interactions, facilitating informed decision-making. With BI, companies can pinpoint inefficiencies, monitor key performance indicators (KPIs), and optimize resource allocation, resulting in lower operational costs and improved product quality.
Moreover, real-time data visualization and predictive analytics help manufacturers anticipate disruptions, refine maintenance schedules, and streamline production processes, enhancing agility and responsiveness in a competitive landscape.
According to a report by Statista, the BI software market is rapidly expanding, projected to exceed $36.35 billion by 2029. This growth is primarily driven by the manufacturing sector’s increasing reliance on data analytics to address the complexities introduced by Industry 5.0 technologies. As manufacturers adopt advanced systems like IIoT and AI, the demand for robust BI tools continues to climb. These solutions empower organizations to effectively harness big data, promoting a culture of continuous improvement and innovation.
Additionally, integrating BI with other technologies fosters better collaboration and communication across departments, ensuring that all stakeholders can utilize data for strategic planning and operational excellence. This interconnected relationship between BI software and the manufacturing industry highlights the critical role of data-driven strategies in achieving sustainable growth.
Key Integrations of Business Intelligence in Manufacturing
Manufacturing businesses rely on key integrations of business intelligence to connect systems such as ERP, MES, and CRM. These integrations facilitate seamless data flow and provide comprehensive insights across operations. Let’s have a look at those.
ERP Systems
Integrating manufacturing ERP and business intelligence allows manufacturers to access real-time insights into their finances, inventory levels, and production schedules, which enhances their decision-making processes.
Supply Chain Management
When BI is integrated with supply chain management systems, it enables better demand forecasting, inventory optimization, and supplier performance analysis, ultimately leading to more efficient operations.
IoT Devices
Connecting BI tools with Internet of Things (IoT) devices allows manufacturers to monitor equipment performance, track production metrics, and implement predictive maintenance strategies effectively.
Quality Management Systems
Integrating BI with quality management systems helps manufacturers analyze quality data, identify defect trends, and take timely corrective actions to improve overall product quality.
Customer Relationship Management (CRM)
Linking BI with CRM systems provides manufacturers with valuable insights into customer preferences, sales trends, and market demands, driving more effective marketing strategies and product development.
Human Resource Management Systems (HRMS)
By integrating BI with HRMS, manufacturers gain insights into workforce performance, training requirements, and employee turnover rates, facilitating better talent management.
SCADA Systems
Connecting BI with Supervisory Control and Data Acquisition (SCADA) systems enables manufacturers to monitor and manage industrial processes, offering insights into operational performance and supporting real-time decision-making.
MES (Manufacturing Execution Systems)
Integrating BI with Manufacturing Execution Systems (MES) allows manufacturers to analyze production data, monitor work in progress, and optimize manufacturing processes, resulting in improved efficiency and reduced waste.
EAM (Enterprise Asset Management)
Linking BI with Enterprise Asset Management (EAM) systems enables manufacturers to assess asset performance, anticipate maintenance needs, and optimize resource utilization, ultimately improving reliability and minimizing downtime.
Benefits of Business Intelligence for Manufacturing: Unlocking Enhanced Efficiency and Collaboration
BI systems transform the manufacturing landscape by providing critical insights that lead to smarter, faster, and more effective decision-making. Here’s how BI can specifically benefit your manufacturing operations:
Enhanced Quality Control
BI systems support real-time monitoring of production quality, enabling manufacturers to identify issues as they arise. By employing quality metrics and dashboards, companies can detect defects early in the production process, minimizing scrap and rework costs.
This proactive approach to quality management cultivates a culture of continuous improvement, ensuring that products consistently meet or exceed customer expectations and comply with regulatory standards. Additionally, effective quality control enhances brand reputation and fosters customer loyalty, both of which are essential for long-term success.
Supply Chain Optimization
Business intelligence in manufacturing improves visibility across the entire supply chain, allowing manufacturers to analyze supplier performance, lead times, and inventory levels effectively. This comprehensive perspective enables better coordination with suppliers and distributors, resulting in more efficient procurement processes.
Manufacturers can cut costs, enhance service levels, and boost their responsiveness to market demands by optimizing supply chain operations. Greater agility and transformation within the supply chain not only supports faster product delivery but also allows manufacturers to adapt more readily to changes in customer preferences or market dynamics.
Data-Driven Decision Making
The utilization of business intelligence for manufacturing can convert raw data into meaningful insights, enabling manufacturers to base their decisions on real-time information. This approach minimizes dependence on intuition or outdated reports, ensuring that strategies are aligned with current market conditions and operational performance.
With enhanced visibility into crucial metrics, decision-makers can swiftly identify trends and respond proactively, which significantly enhances agility in the manufacturing process. Consequently, organizations can better align their operations with overall business objectives, fostering a culture focused on accountability and high performance.
Enhanced Collaboration
Manufacturing business intelligence promotes collaboration across various departments by providing a unified view of data. With shared dashboards and reports at their disposal, teams can communicate more effectively and align their objectives seamlessly.
This collaborative atmosphere encourages cross-functional problem-solving and innovation, leading to more cohesive strategies that propel overall business success. By dismantling silos within the organization, diverse perspectives and expertise can be leveraged, cultivating a more innovative culture that drives ongoing improvement.
Cost Reduction
By optimizing processes and enhancing resource allocation, the utilization of business intelligence in the manufacturing industry leads to substantial cost savings in operations. Improved efficiency, reduced waste, and better inventory management collectively result in lower operational expenses.
Additionally, informed decision-making can pave the way for smarter investments and more cost-effective strategies, ultimately enhancing the company’s overall profitability and financial health. This focus on cost reduction not only strengthens the bottom line but also provides manufacturers with the financial flexibility to invest in innovation and growth initiatives.
Improved Operational Efficiency
Through the analysis of performance metrics, manufacturers can effectively identify bottlenecks and inefficiencies in their processes. BI manufacturing tools deliver comprehensive insights into production workflows, empowering organizations to streamline operations and eliminate waste. This process optimization not only results in quicker turnaround times but also reduces costs linked to delays and excess inventory.
Improved operational efficiency leads to better utilization of both machinery and labor, allowing manufacturers to increase output without compromising quality or incurring additional costs.
Use Cases of Business Intelligence for Manufacturing
Business Intelligence is essential in modern manufacturing, impacting all aspects of operations. Let us explore real-world examples of how top manufacturers use BI to enhance production efficiency, ensure product quality, and increase operational effectiveness:
General Electric (GE) Employment of Predictive Maintenance
Predictive maintenance utilizes Business Intelligence (BI) tools to analyze historical and real-time equipment data, allowing manufacturers to foresee potential failures. This proactive approach enables the scheduling of maintenance activities before issues arise, minimizing unplanned downtime and optimizing resource allocation.
General Electric (GE) employs predictive maintenance in its aviation division by continuously monitoring data from aircraft engines. By analyzing factors such as temperature and vibration, GE can forecast potential failures and alert operators to perform maintenance proactively. This strategy significantly reduces downtime and maintenance costs while enhancing the safety and reliability of their aircraft.
Siemens’ Global Business Services
BI tools can greatly improve factory operations by delivering customizable digital services tailored to specific organizational requirements. By integrating data from diverse sources, BI enables manufacturers to create applications that streamline production processes. This empowers decision-makers to utilize data in ways that address their unique challenges, facilitating more effective management of both financial and operational workflows.
Siemens Global Business Services (GBS) demonstrates this use case through its Record-to-Report (R2R) service, which provides BI as a customizable digital solution. By developing and implementing tailored applications, Siemens assists factory decision-makers in optimizing processes wherever data is accessible. This capability allows organizations to apply predictive analytics for managing financial and production activities, ultimately improving efficiency and enabling informed decision-making throughout their operations.
Boeing’s Implementation of BI for Quality Control
Business Intelligence empowers manufacturers to monitor production quality in real time, facilitating immediate corrective actions when defects are detected. This proactive strategy ensures that quality issues are resolved quickly, minimizing their impact on production and maintaining overall product integrity.
Boeing employs BI tools to track quality metrics throughout its production lines. By analyzing data from various checkpoints in the manufacturing process, Boeing can identify patterns and trends in defects that may highlight underlying problems. This analytical approach enables the company to make timely adjustments, improving product quality and significantly decreasing the need for rework, ultimately leading to enhanced efficiency and increased customer satisfaction.
Toyota’s Production Efficiency with BI
Business Intelligence (BI) tools play a crucial role in enhancing production efficiency by allowing manufacturers to monitor operations in real-time and swiftly address issues. By incorporating data analytics into the production process, manufacturers can pinpoint bottlenecks, track quality metrics, and make data-driven decisions that streamline workflows.
Toyota, through its Toyota Production System (TPS), effectively utilizes BI to optimize efficiency and quality. Central to TPS are the principles of Jidoka and Just-In-Time, which empower workers to stop the production line by pulling the andon whenever a defect is detected. BI tools support real-time monitoring of production data, enabling rapid identification and resolution of problems.
Additionally, the Just-In-Time approach ensures that Toyota manufactures only what is necessary based on customer demand, enhancing overall operational efficiency while maintaining high-quality standards for every vehicle produced.
Intel’s Utilization of BI for Analyzing Supply Chain Data
Business Intelligence (BI) tools streamline supply chain risk management by providing in-depth data analysis and insights. These tools help supply chain managers identify potential risks by examining historical and real-time data, such as supplier performance and market trends. By integrating both structured and unstructured data, BI offers a holistic view, making it easier to pinpoint the root causes of disruptions.
For example, Intel’s supply chain managers leverage BI to investigate and analyze supply chain data, focusing on risk identification and root cause analysis. When geopolitical events caused disruptions, they employed BI tools to analyze data from various sources, including ERP systems and social media. This in-depth analysis allowed Intel to identify supplier performance issues and evaluate alternative sourcing options, ultimately reducing risks and enhancing supply chain resilience.
Best Practices of Adopting BI For Manufacturing
Implementing Business Intelligence in manufacturing requires careful planning and execution to fully capitalize on its potential. Here are the best practices to follow to ensure successful adoption and optimal use of Business Intelligence for manufacturing processes:
Set the Stage and Craft Clear BI Objectives
Establishing precise objectives is fundamental to a successful BI implementation. Begin by identifying targeted goals that align with your broader business strategy, such as enhancing operational efficiency or improving product quality.
Clearly define key performance indicators (KPIs) that will measure your success and provide clarity on expected results. It’s essential to involve all relevant stakeholders to ensure alignment and buy-in. Regularly reviewing and adjusting these objectives based on performance metrics will help keep your BI initiatives relevant and impactful.
Engage Key Players or Stakeholders
Involving stakeholders from various departments is crucial for the effective adoption of business intelligence in the manufacturing industry. Start by engaging department leaders and key users early on to gather insights into their specific BI requirements and expectations. Organize workshops to promote collaboration between IT and business units, ensuring everyone understands the benefits of the BI solution.
Establish a feedback loop that allows stakeholders to share experiences and suggest enhancements. This collaborative approach not only strengthens the BI strategy but also cultivates a culture centered around data-driven decision-making throughout the organization.
Invest in Data Quality
The success of any BI manufacturing initiative is heavily reliant on the quality of the data utilized. Implementing comprehensive data governance policies is essential for ensuring data accuracy, consistency, and reliability. Conduct regular audits of data sources to maintain integrity and standardization across your organization.
Encourage a sense of data stewardship by empowering employees to take ownership of the data they handle. Leverage specialized tools designed for data cleansing and validation to enhance overall quality. By prioritizing data integrity, manufacturers can derive more valuable insights and make informed decisions.
Choose the Right BI Tools
Selecting the appropriate BI tools is vital for achieving your desired objectives. Assess both current and future BI manufacturing needs to ensure the tools you select will grow alongside your organization. Prioritize user-friendly interfaces that facilitate broader adoption among employees.
Verify compatibility with existing systems to avoid integration challenges and consider solutions that offer scalability to accommodate future requirements. Additionally, evaluate vendor support and community resources to ensure ongoing assistance and knowledge sharing. The right tools can significantly enhance the effectiveness of your BI initiatives.
Start with a Phased Approach
Adopting a phased approach to BI implementation can lead to greater success. Initiate a pilot project that focuses on a specific area within your manufacturing operations, allowing you to demonstrate value and gather critical insights. Use this pilot to refine processes and identify potential challenges before a full-scale rollout.
Gradually expand your BI capabilities to other departments based on the lessons learned. This incremental strategy minimizes risk and builds a strong foundation for a comprehensive BI plan, enabling you to adapt your tactics as necessary.
Monitor and Iterate
Ongoing assessment and iteration are vital for optimizing your BI for manufacturing initiatives. Regularly evaluate the performance of BI tools and gather user feedback to identify areas for enhancement. Solicit input from users to inform adjustments in processes and tools, ensuring that the BI system evolves alongside changing business needs.
Stay informed about industry trends and advancements in BI technology to enhance your strategy continually. An agile approach allows your organization to remain adaptable and responsive, maximizing the impact of your BI efforts.
Integrate with Existing Systems
Achieving seamless integration of BI tools with existing systems is essential for maximizing data utilization. Ensure that manufacturing BI software can effectively connect with ERP, CRM, and other relevant platforms. Map data flows between systems to facilitate efficient data sharing and reporting.
Provide training on integrated workflows to boost productivity and ease of use. Regularly review the performance of these integrations to identify optimization opportunities, ensuring that all systems collaborate harmoniously for better insights.
Train Your Team
Providing thorough training is essential for the successful adoption of BI tools. Develop training programs tailored to address the unique needs of different user roles within the organization. Offer continuous support and resources to help employees gain proficiency in utilizing BI tools effectively.
Cultivating a culture of data literacy is crucial, as it empowers team members to leverage data in their decision-making processes. Promote knowledge sharing among colleagues, and consistently assess the effectiveness of training programs to ensure ongoing improvement.
Monitor and Measure Progress
Consistently tracking and evaluating performance is essential for understanding the effectiveness of your BI initiatives. Define KPIs to measure progress against your established objectives, and utilize dashboards to visualize these metrics effectively. Conduct regular reviews to identify patterns and opportunities for enhancement, ensuring that your strategies stay aligned with overarching business goals.
By consistently measuring progress, you can make data-driven adjustments that enhance the overall impact of your BI efforts. Furthermore, encourage team members to share their insights based on their observations, promoting a culture of continuous improvement. This collaborative approach not only fosters accountability but also inspires innovation within your BI processes.
Implementing BI in Manufacturing: Key Challenges and Practical Solutions
Adopting Business Intelligence for manufacturing solutions comes with its set of challenges that can impact the success of its implementation. In this section, we explore some of the common hurdles manufacturers face and the practical solutions to overcome them:
Change Management
Shifting to a BI-driven approach requires significant changes in processes and organizational culture, which can face resistance from employees who are used to traditional methods.
Solution: Developing a clear change management strategy is essential for facilitating smooth transitions. This strategy should engage stakeholders at all levels, include communication plans highlighting BI’s advantages, and promote incremental implementation of changes. Such an approach can reduce anxiety about the transition and encourage staff to embrace new practices.
Data Integration
Manufacturing operations often involve a variety of systems—such as ERP, MES, and CRM—that generate data in different formats. This diversity can create silos, making it difficult to consolidate and analyze data cohesively.
Solution: To overcome this challenge, manufacturers can implement middleware or specialized data integration tools designed to facilitate seamless data aggregation. Additionally, adopting standardized data formats across systems can enhance compatibility, ensuring that all data sources work together effectively for unified analysis.
User Adoption
Even the most advanced BI tools can fail if users do not embrace them. Resistance may stem from a lack of understanding or fear of new technology, hindering effective utilization.
Solution: Investing in comprehensive training programs is crucial for fostering user adoption. These programs should not only cover the technical aspects of BI tools but also emphasize their practical benefits. Demonstrating early successes and encouraging a culture that values data-driven decision-making can further increase engagement and buy-in from employees.
Data Quality
Inconsistent or inaccurate data can significantly undermine BI efforts, leading to misguided insights and poor decision-making. Poor data quality often arises from manual data entry errors or outdated information.
Solution: Establishing robust data governance as well as manufacturing business intelligence best practices is essential to maintain high data quality. Regular data audits, validation processes, and automated data cleaning can help identify and rectify inaccuracies. Implementing a centralized data management system can also enhance data consistency and reliability across the organization.
How Can Appinventiv Help You in Leveraging Business Intelligence to Make Data-Driven Decisions for Your Manufacturing Business?
At Appinventiv, we excel in transforming complex data into actionable insights that streamline and enhance your manufacturing operations. Being a dedicated manufacturing IT services provider, our process begins with a deep dive into your existing systems to fully understand your specific challenges and needs. We then develop a custom software solution that is tailored precisely to integrate seamlessly with your current software, including ERP systems and other critical manufacturing applications.
As a renowned business intelligence services company, our customized approach ensures that you receive a BI solution that is not only fit for purpose but also enhances decision-making capabilities across your production lines, supply chain management, and quality control processes. With these tailored insights, you can achieve higher efficiency, reduce costs, and improve product quality.
Furthermore, our team of experts continuously works to refine your manufacturing business intelligence solutions, ensuring they deliver the maximum benefit by identifying new opportunities for efficiency and growth. This proactive approach helps you stay ahead of technological trends and maintain a competitive edge in the manufacturing industry.
Get in touch with us to empower your manufacturing business with the intelligence to make faster, smarter, and more effective decisions.
FAQs
Q. What is business intelligence in manufacturing?
A. BI for manufacturing involves the use of data analytics and reporting tools to enhance decision-making and operational effectiveness. It entails gathering and analyzing data from multiple sources, including production processes, supply chain activities, and market trends. BI allows manufacturers to pinpoint inefficiencies, track quality, and predict demand.
By utilizing real-time insights, businesses can leverage manufacturing business intelligence solutions to optimize production schedules, improve product quality, lower costs, and adapt quickly to market shifts, ultimately boosting competitiveness and profitability.
Q. What are some of the key components of manufacturing business intelligence?
A. Some of the key components of manufacturing business intelligence software are:
- Data Integration: Tools and processes that unify data from various systems (such as ERP, MES, and SCADA) to provide a holistic view of manufacturing operations.
- Performance Measurement: The establishment and tracking of key performance indicators to evaluate operational efficiency, product quality, and workforce effectiveness.
- Data Warehousing: A centralized system that collects and stores data from multiple sources, allowing for comprehensive analysis and reporting across the organization.
- Supply Chain Analytics: Tools that analyze supply chain data to improve forecasting, manage supplier performance, and optimize logistics for enhanced efficiency.
- Mobile BI: Applications that allow users to access BI insights on mobile devices, ensuring decision-makers can stay informed and responsive while on the move.
Q. How is BI used in manufacturing?
A. Here are some of the ways through which business intelligence in manufacturing can be utilized across the industries: .
- Quality Control: Analyze metrics to detect defects and trends, enabling timely corrections.
- Predictive Maintenance: Forecast equipment failures to reduce downtime.
- Informed Decision-Making: Leverage data for improved competitiveness and operational performance.
- Real-Time Monitoring: Quickly identify and resolve production issues.
- Supply Chain Optimization: Gain insights into inventory levels and supplier performance.
- Demand Forecasting: Utilize historical data to anticipate customer needs.
- Cost Analysis: Assess production costs for better budgeting and resource allocation.
Q. What are some of the top BI tools for the manufacturing industry?
A. Here are some of the top tools that redefine the business intelligence for manufacturing industry:
- MicroStrategy: Offering enterprise-level analytics, MicroStrategy includes robust data discovery tools, mobile analytics, and excellent integration capabilities across diverse data sources.
- Tableau: Renowned for its powerful visualization features, Tableau allows users to craft interactive dashboards that deliver real-time insights from multiple data sources.
- IBM Cognos Analytics: This all-encompassing BI tool excels in data preparation and visualization, leveraging AI for automated insights and enhancing data discovery processes.
- Power BI: With its intuitive drag-and-drop interface, Power BI integrates seamlessly with Microsoft products, providing robust reporting and easy sharing functionalities.
SAP Analytics Cloud: Merging BI, planning, and predictive analytics, SAP Analytics Cloud is one of the most common examples of BI in manufacturing. The tool is tailored for organizations utilizing SAP solutions, offering real-time access to data visualizations.
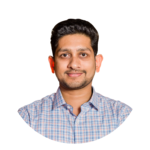
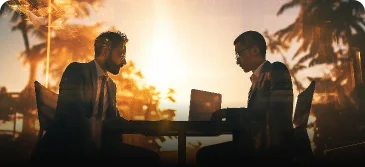
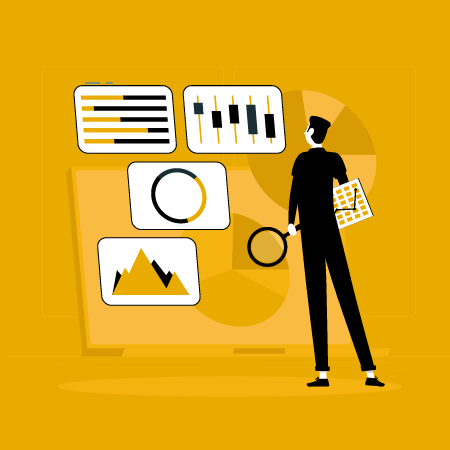
How data mining helps in business intelligence
Data is the life-powering proverbial blood that empowers the corporate economy of the 21st century. And although it may incite fanciful scenarios to mind with a mere mention, the truth is data is key to unlocking human productivity in every sphere of life. Climate change, business failures, epidemics, and crop production, all can be understood…
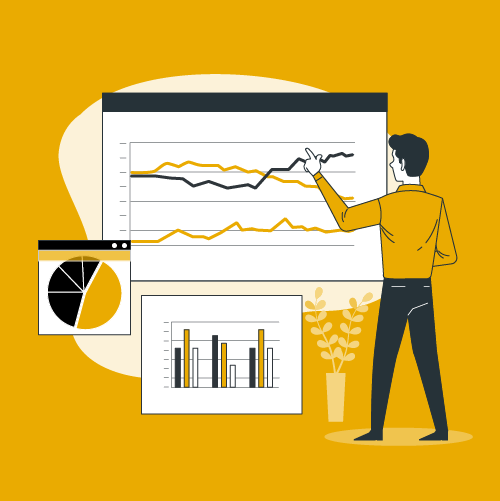
BI for financial services - How to build a successful BI strategy for your FinTech business?
Considering the volume of data financial service sectors disperse across applications, achieving a 360-degree view of customers and business as a whole can be challenging. This is where business intelligence for financial services comes into play. A robust BI solution for a financial services business helps convert a large amount of data into actionable insights.…

How Business Intelligence Benefits the Retail Industry
Retail is one of the most data-driven industries globally, so using business intelligence tools to understand customer behavior, estimate inventory needs, and build forecasts is the life’s blood of any retailer. BI helps retailers organize, analyze, and contextualize business data from around the company. It also provides reports, performance measures, and company trends that help…